Manufacturing defects of tablets, also known as core tablet defects are related to imperfections in any one or more of the following factors:
- Tableting process
- Excipients
- Machine
Manufacturing defects of tablets may cause damage to the production schedule, labor effort, and consequently loss of money. So, manufacturing defects of tablets are an important issue for a pharmaceutical company. Usually, an industrial pharmacist encounters a number of manufacturing defects in tablets. An industrial pharmacist needs to know what the reasons behind the manufacturing defects of tablets are. You may also read 21 tablet defects of tablets.
Common manufacturing defects of tablets
Process-related Manufacturing defects of tablets
Capping: Capping is either partial or complete separation of the top or bottom crowns of a tablet from the main body of the tablet during the ejection of the tablet press or during subsequent handling.

Capping is one of the common manufacturing defects of tablets that may occur during tableting due to the following reasons:
- Air entrapment in the granular material or
- A large amount of fines in the granulation or
- Insufficient amount of binder or improper lubricant.
Lamination / Laminating: Lamination is the separation of a tablet into two or more distinct horizontal layers.
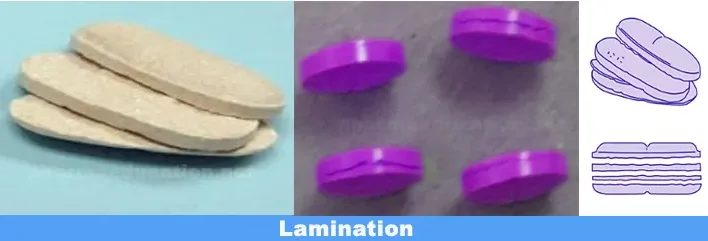
It is a manufacturing defect of tablets that may occur during tableting due to the following reasons:
- Air- entrapment in the granular material or
- Oily/waxy material in granules or
- Too much hydrophobic lubricant or
- Rapid decompression
Cracking: Small, fine cracks observed on the upper and lower central surface of tablets, or very rarely on the sidewall are referred to as cracking. It is a manufacturing defect of tablets that may occur during tableting due to the rapid expansion of tablets when deep concave punches are used or large-size granules or too dry granules.
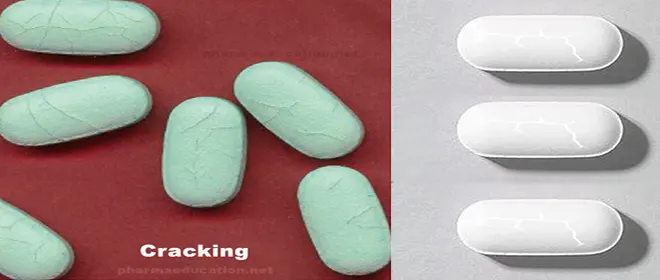
Weight Variation: Weight variation is a problem due to unequal size and distribution of the granules or poor flow of granules from the hopper to die through the feed frame.
Hardness Variation: The hardness of the tablet does not remain constant but it has a limit. It is one of the manufacturing defects of tablets that may occur during tableting due to unequal size and distribution of the granules or improper drying of granules or poor flow of granules from the hopper to die through the feed frame.
Excipient-related defects of tablets
Chipping: Chipping is the breaking of tablet edges during the pressing process or during the subsequent handling and coating. It is a manufacturing defect of tablets that may occur during tableting due to very dry granules or sticking on punch faces or too much binding.
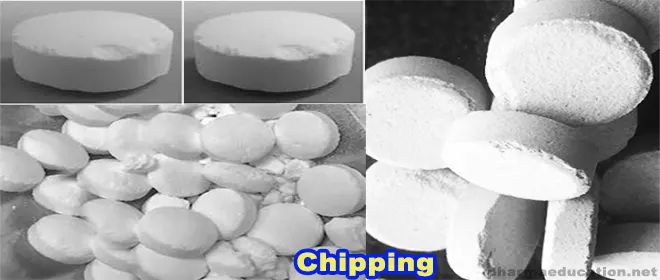
Sticking: Sticking is the adhesion of tablet material to the die wall. It is due to the excess moisture in granules or improper lubricants or too much binder or hygroscopic granules material. Filming is a slow form of sticking and is largely due to excess moisture in the granulation.
Picking: Picking is a condition where a small surface of tablet material is removed by the punch and adheres to the surface of the punch face. It is a manufacturing defect of tablets that may occur during tableting due to improper drying or improper lubricant or too much binder or rough punch face.
Binding: Binding is the condition where a tablet adheres, seizes or tears in the die or a film is formed on the die area and hindered the ejection of the tablet. It is a manufacturing defect of tablets that may occur during tableting due to excessive binder or too moist granules or improper lubricant or rough die.
Mottling: Mottling is an unequal distribution of color on a tablet, with the appearance of light and dark areas on it. It is a manufacturing defect of tablets that may occur during tableting due to improper mixing or using a color drug along with colorless/ white excipients.
Machine-related Manufacturing defects of tablets
Double Impression: Double impression is machine related problem where a monogram or engraving shape or break line appears twice on the tablet surface. It is a manufacturing defect of tablets that may occur during tableting due to the free rotation of the punches having some engraving on their faces.
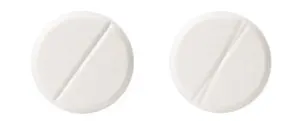
In summary, almost most of the manufacturing defects of tablets may occur because of one or more reasons and they may be formulation, machine, or process related.
Also, read: Sweetening agents used in Pharmaceutical Preparations, Disintegrants Used in pharmaceutical preparations.